How To Choose a Proper Chemical Storage Building
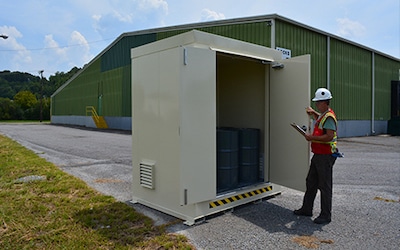
Updated: May 8th, 2024
Choosing a proper chemical storage building for your application can be intimidating. Regulators, insurance underwriters, and safety officials have strict standards, while suppliers provide numerous options with varying degrees of expertise. Disregarding regulations can become very costly as well.
The Occupational Safety and Health Administration (OSHA) holds companies accountable for creating and maintaining a safe working environment. In 2023, OSHA fined a Missouri chemical plant $393,000 for accruing 16 violations after receiving 24 violations in 2021.
Investigations revealed some of these violations stemmed from placing their employees at risk of exposure to dangerous chemicals, including ethylene oxide. They also had an inadequate medical evaluation procedure for employees exposed to this chemical.
Situations like this may prompt you to wonder: how can you keep employees safe and meet regulatory requirements at a reasonable cost? There are many types of buildings with various features. How do you know which one is right for your needs?
Follow these 5 steps to choose the right chemical storage building for you:
How to Choose a Chemical Storage Building
Step 1: Identify Your Chemicals and Their Hazards
Suppliers issue a Safety Data Sheet (SDS) with every chemical. It describes the properties of the chemical and the hazards associated with it. how can you keep employees safe and meet regulatory requirements at a reasonable cost? There are many types of buildings with various features. How do you know which one is right for your needs? Depending on their location in proximity to other occupied buildings or property lines, chemical storage buildings may require fire-rated construction. Flammables and other chemicals with low flash points will need explosion-proof electrical components. Exhaust fans, fire suppression, and other components could be required to remain compliant with local and national regulations. Always consult with your local code authority.Step 2: Decide on Your Storage Location
International Building Code (IBC), NFPA, OSHA, and other governing bodies set requirements for the proper storage of any chemicals, including flammables, combustibles, corrosives, oxidizers, organic peroxides, pesticides, etc. Wall construction requirements depend on the proximity of the chemical storage to occupied buildings and property lines. Remember, right-of-way buffer zones count as property lines. Select a fire rating for your chemical storage building based on these general criteria:- 4-hour fire rating when placed within 10 feet outside of or inside an occupied building
- 2-hour fire rating when placed between 10 and 30 feet outside and away from other property
- Non fire-rated for outside placement more than 30 feet away from other buildings or property
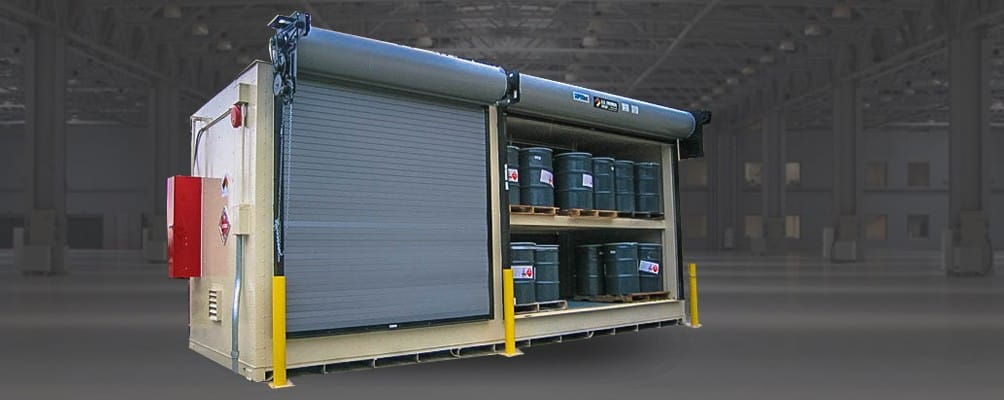
Step 3: Determine Your Storage Volumes and Weight
To determine the proper building size and footprint, you must identify the types and numbers of containers to be stored. Understanding the inventory ensures the size of the building and the spill containment are compliant and optimal for your application. U.S. Chemical Storage buildings feature elevated flooring. This is due to the secondary containment sump underneath, which catches spills. Select the standard elevated flooring with a load rating of 500 lb. psf, or specify a higher rating according to your needs. Standard widths and lengths of chemical storage buildings are 6-, 8-, 10- and 12-feet, but they can extend up to 52 feet. Choose a combination of standard units or customize a building to the size you need.Step 4: Specify Your Openings, Racks, and Shelving
The design of a chemical safety building should make transferring chemicals easy. Customers can specify the number of openings, choose entry ramps or steps as well as racks or shelving systems. Multi-tier racks are available for totes and pallets or drums. Their heavy gauge construction makes them capable of enduring long years of daily wear and tear, loading and unloading. Select horizontal drum racks for gravity dispensing. Choose sump shelving to contain small leaks and spills on the shelf. It is easier to clean a small shelf spill than a large spill in the secondary containment sump. Durable and strong, the steel construction handles heavy load requirements for smaller-sized containers.Step 5: Make Sure You Have Spill Containment
Secondary containment is an integrated sump that catches spills and leaks inside the building. U.S. Chemical Storage buildings offer Environmental Protection Agency (EPA) and OSHA-compliant sumps. Standard spill containment sumps are made using continuously welded 10-gauge steel sheets at the base, as well as structural steel tubing, to create the vertical walls for the containment. Each U.S. Chemical Storage sump is tested at the factory to be leakproof. Sumps prevent spills from leaving the building and polluting the environment. <Contact Us
Contact U.S. Chemical Storage to learn how to choose a proper chemical storage building that fits your needs. Our professional consultants help you find the best solution for your application and discuss your building options with you. We provide free quotes of solutions that meet regulatory requirements and protect your assets, employees, and local environment. References:- U.S. Department of Labor, US DEPARTMENT OF LABOR PROPOSES $393K IN FINES AFTER FOLLOW-UP INSPECTION FINDS VERONA, MISSOURI CHEMICAL PLANT CONTINUES TO ENDANGER WORKERS
- U.S. Chemical Storage Fire Suppression
- U.S. Chemical Storage Accessories